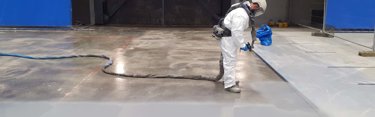
AdlerCoat™ polyurea and epoxy coatings
We help organisations actively reduce maintenance costs, extend the life of their assets, and prevent corrosion, dirt, and contamination with our durable AdlerCoat™ polyurea and epoxy coating solutions.
100% waterproof and hydrocarbon resistant, AdlerCoat™ are flexible monolithic membranes that help to protect the environment and your assets against deterioration, degradation, and structural weakness.
For complete leak prevention of oils, hydrocarbons, fuels, solvents, aggressive chemicals, and gases, AdlerCoat™ can contain chemical spills for up to five days.
The AdlerCoat™ range includes
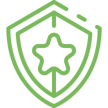
AdlerCoat™ Standard
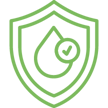
AdlerCoat™ Performance
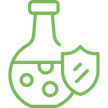
AdlerCoat™ Chemical
Typical applications for AdlerCoat™ Standard include:
- Primary and secondary containment for hydrocarbon storage
- Fuel loading and unloading stations
Typical applications for AdlerCoat™ Performance include:
- Containment of wastewater or effluent
- Containment of weak chemicals
- Spill control
- Water ponds
- Vapour barriers
AdlerCoat™ Chemical is an exceptional solution for chemical and pharmaceutical industries
- Tested (up to 72 hours exposure guarantee)
- Superb protection against a wide variety of chemicals
- Resistant to more products than other available coatings
- Vinylester glassflake system
- Suitable for a variety of applications
- Dedicated technical support post-install
Features and outputs
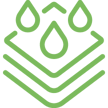
Waterproof
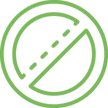
Zero volatile organic compounds
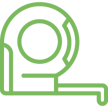
100% solids

Flexible
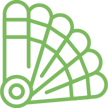
Branded
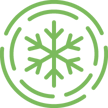
Impact resistant
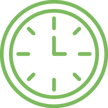
Time-saving
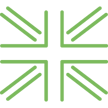
Made in the UK
AdlerCoat™ is relevant in the following sectors
- Energy: Oil and gas, the electric grid, nuclear, wind, hydro-electric
- Infrastructure: Water (wastewater), commercial, industrial, defence
- Engineering: OEM, custom product formulations, toll blending, bedliners and equipment coatings, industrial flooring
- Transportation: Chemical, hazmat, hydrocarbon, oils
- Environmental: Groundwater protection, waste, encapsulation, soil stabilisation, mining
How is AdlerCoat™ applied?
The first stage before we apply the coating is to ensure the surface is clean and dirt free, with no loose materials. We remove algae growth, potential contaminants and fibral material either mechanically using the high-pressure jet wash, or manually by wiping down the surface.
Once the surface is clean, we perform any minor repairs such as concrete patch repairing, sealing any potentially weak joints or areas, and sealing any cracks.
The next stage is to apply the primer coat. A small aggregate is broadcast into the primer while it is going off to act as a key between the surfaces. Once the primer has gone off, we remove any excess grit from the surface and clean any dust or dirt.
Now we are ready to apply AdlerCoat™. AdlerCoat™ Standard and AdlerCoat™ Performance is sprayed in one layer over the top and the edges are sealed. AdlerCoat™ Chemical is applied in multiple layers beginning with a primer, followed by a base, three layers of glassflake, and a topcoat.
If anti-slip is required, this can be added to the chemical topcoat. The penultimate coat would include a layer of aggregate with a stippled effect to make it non-slip. Non-slip is also possible with AdlerCoat™ Standard and AdlerCoat™ Performance.
You might also be interested in...
Keep your business compliant and protect the environment while reducing the risk of operational downtime
Find out how Adler and Allan reduce your risk and support you on your journey to Net-Zero through the management and maintenance of assets.
Contact our experts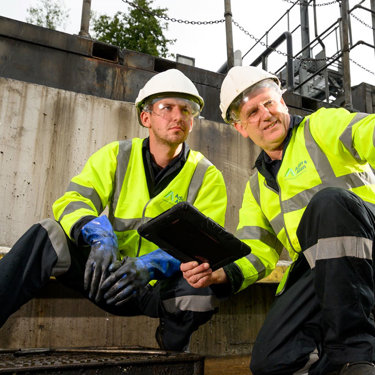