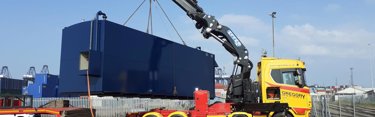
Storage tank design and installation
Ready to discuss your project?
Please leave your details and a member of our team will reach out to discuss your requirements in more detail and arrange next steps.
We help storage tank and tank farm operators with the design and installation of bespoke and off-the-peg storage tanks, so you can remain compliant with all relevant standards, good practice, and regulations.
Our end-to-end fuel tank installation service provides full site surveys, expert tank configuration recommendations, civil engineering, and proven pollution prevention measures.
Legislation
GPP2 Above Ground Oil Storage
There are recognised British Standard and trade association tank standards for different types of tanks. Your tank manufacturer, supplier or installer should advise you on the minimum design and manufacturing standards under the appropriate accredited quality assurance scheme.
Please note that compliance with standards for construction and manufacture doesn’t guarantee compliance with OSR. Other aspects such as secondary containment, pipework, location, and deliveries, also affect OSR compliance.
Choose a tank that:
- Is expected to last at least 20 years, with proper maintenance (see Section 12), before it needs to be replaced.
- Is made of a material that is suitable for the type of oil you will store (check with supplier).
- Is of sufficient strength and structural integrity to ensure that it won’t burst or leak in ordinary use.
- Has a way of preventing drain down by gravity e.g. top off-take and / or isolating check valves.
API 650
API 650, Welded Tanks for Oil Storage, is a standard developed and published by the American Petroleum Institute (API) that establishes minimum requirements for the design, fabrication, erection, and inspection of welded storage tanks. It is designed to ensure the safety, sustainability, and environmental performance of oil storage tanks.
API 650 is widely used for tanks designed to withstand low internal pressures (2.5 PSI), for the storage of typical products such as crude oil, gasoline, chemicals and produced water.
Features and outputs
- In house civils engineering team can design and install your storage tank to your unique specifications and in-line with current legislation.
- Compliant with GPP2 and API 650.
- Design and installation of bespoke and off-the-peg tanks.
Added value
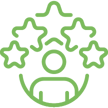
Expertise
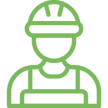
Experience
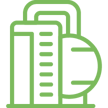
Associated items
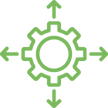
Additional services
Investigation
Our experts will investigate your site and specific requirements before creating a structural design for your asset. Our services include:
- API inspection
- Tank venting assessments and calculations
- Equipment suitability assessment
- Equipment condition reporting
- Regulatory compliance
- Project management
- HAZOP studies
- DSEAR/ATEX Compliance & explosion protection documentation
- Hazardous area identification
Excavation
If excavation is required, it is undertaken in line with relevant regulations. If the tank needs to be below 1.2 metres underground, it will require shoring. Our experts will install drag box shuttering, sheet pile and whale shuttering to ensure the surrounding soil doesn’t collapse the tank. They can also install dewatering systems if the water table too high.
Install underground tanks
The next stage is to install and construct a concrete pad underground to accommodate the specific weight of the tank. Anchor points will be installed on the concrete pad.
Once the tank has been lifted in, we will secure it to the anchor points using straps before filling in the concrete surround. We need to ensure the correct pressure is maintained inside the tank throughout the install by adding water as the concrete is being poured to avoid damage to the tank.
We then reinstate formwork for the concrete and set the manhole covers. Aesthetically we will either concrete on the top, lay grass, or lay tarmac to match the existing land.
Flame arresters
Flame arresters are passive devices which are fitted within or at the end of a pipeline to prevent the onward travel of a flame path. They are used to contain an incident and protect high-value equipment such as vapour recovery units.
An arrester prevents the propagation of flame from the exposed side of the unit to the protected side using a metal matrix called an element. An element comprises a bundle of narrow metal channels which remove heat from the flame and starve it of oxygen as it attempts to pass through it. The diameter and length of the channels within the element will vary significantly, depending on the flammability of the gas (gas group) the arrester is designed for use with.
We supply and service a wide range of detonation and deflagration flame arresters. Our CompEx-trained engineers can provide advice on the selection and installation of a suitable device and are experienced in servicing arresters made by other manufacturers.
All our flame arresters are:
- Compliant with ISO 16852:2008
- ATEX rated
- Manufactured to ISO9001
- Easy to service
- Cost effective
- Supplied with a document pack which includes certified drawings, test certs, welding specs, material test certs; MIL certs & 3.1 certs
Deflagration flame arresters
These are required where a flame path does not have the potential to travel at supersonic velocities. This is dictated by the position of the arrester - specifically the length of the pipe run between the arrester and the potential source of ignition. A deflagration arrester is typically smaller and lighter than a detonation arrester. Deflagration arresters can also be installed in end-of-line applications and under pressure/vacuum vents.
Detonation flame arresters
Detonation flame arresters are required where a flame path has the potential to travel at supersonic velocities. This is dictated by the position of the arrester, specifically, the length of the pipe run between the arrester and the potential source of ignition. A detonation arrester is designed to withstand the shock and extreme pressures that a supersonic flame path can generate - generally resulting in a larger, heavier unit.
Tank venting
We supply, fit, and service a wide range of pressure and vacuum relief valves for use in tank storage applications.
The devices allow bulk liquid storage tanks to vent during filling, emptying and when thermal effects require, preventing damage, minimising emissions, protecting the environment, and providing significant financial savings.
Emergency relief valves prevent against abnormal internal pressure beyond the capability of the pressure relief vent and costly tank ruptures.
Floating Suction Units
Floating Suction Units (FSUs) draw liquid product from the top of a storage tank rather than from the bottom, avoiding the foreign particles, rust, sludge, and debris which tend to sit near the bottom of a storage tank and resulting in a purer product.
An FSU comprises an inlet which is suspended from floating pontoons so it sits just below the product surface. This inlet is then connected to a tank outlet using a combination of pipes and swivels.
We supply both single and double-jointed FSUs, fitted by our experienced team in horizontal or vertical, above, or below ground storage tanks.
Features include:
- Maintenance-free, lifetime lubricated dual race swivel joints.
- Triple-sealed swivel joints specially designed for submerged service.
- Each FSU is designed to the tank to allow fitment with minimum modifications.
- Available in a variety of different materials and arrangements
- Easy installation, full installation manuals and project support available.
You might also be interested in...
Environmental compliance today, creating a sustainable tomorrow
Helping you reduce risk to the environment and your operation by managing assets compliantly while achieving commercial, ESG, and net-zero goals.
Contact our experts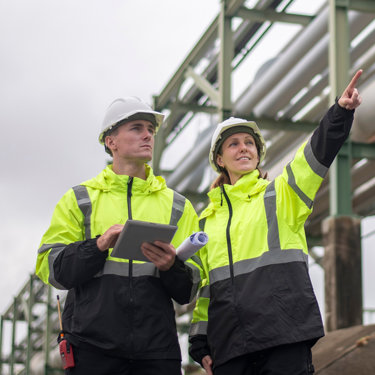