Facilities managers should align separator maintenance to updated schedule 48-03 of SFG20
Published: 6 February 2023
A facilities manager’s go-to guide
SFG20 was developed and created in the early 90s by the Building Engineering Services Association (BESA) and is widely recognised as the industry standard for building maintenance specifications. It’s a database which contains over 2,000 maintenance schedules for more than 70 equipment types, which are constantly reviewed and updated by BESA.
This readily accessible database saves facilities managers the time and hassle of having to find manufacturer guidelines for each individual asset to keep it compliant and operational.
What has changed?
Each schedule (section) includes step-by-step tasks of what is required to maintain each asset, the frequency with which each task should be performed, and what skills are required from the engineer in order to complete the task.
Facilities managers can find it challenging to stay up to date with constantly changing legislation and regulation.
Schedule 48-03
Schedule 48-03 of SFG20 covers the basics of responsible separator maintenance. It advises on which aspects should be checked, how to report any significant deterioration, cleaning any contamination, checking for obstructions in chamber interconnectors and vent pipes, and complying with safety regulations regarding working in confined spaces.
While separator maintenance is not driven by direct legislation, there is an overall requirement under environmental law to prevent pollution from your operations. Part of this obligation is to ensure pollution control devices, like separators, are maintained and continue to work as designed.
Substantial changes to schedule 48-03
There has been a recent change to schedule 48-03 to reflect the maintenance schedule established in the current British Standard for the operation and maintenance of separators, BS EN 858-2:2003 Separator systems for light liquids (e.g. oil and petrol).
The updated schedule 48-03 states that separators must:
- Be fitted with an automatic warning device/high level alarm
- Be serviced and maintained as a minimum on a 6-monthly basis
- Be subject to a maximum interval of a 5-yearly integrity test
- Have full service and maintenance records available for inspection
It’s time to change
Due to these changes, all facilities managers should adjust their separator maintenance schedules to demonstrate their clients have met their statutory obligations.
A pollution incident caused by poorly maintained or inadequate containment is a strict liability offence and failure to adhere to current standards is a key factor in prosecution.
The onus is on facilities managers and their clients to demonstrate they have done their utmost to ensure compliance according to schedule 48-03 of SFG20, as well as BS EN 858-2:2003. To this end, they need to keep comprehensive service logs as evidence of robust maintenance and servicing.
Penalties and reputational issues
The costs of failing to follow the guidance set out in schedule 48-03 of SFG20 are not just environmental, but could be financial and reputational.
Following an increased number of pollution incidents where failed interceptors have been the cause or exacerbating factor, the authorities have been clamping down on poorly maintained and non-compliant operations. Fines can be up to 100% of pre-tax profits and, in certain circumstances, senior officers of offending businesses have been held personally liable.
Long lasting, better performing assets
Ensuring that separators are regularly checked and maintained is essential in demonstrating to the regulatory bodies that you have reduced risk and consequences from failure.
An environmental partner can guide you through this process, ensure records are maintained and stored, and provide remedial works if required.
With more regular checks and inspections made to separators, this should ensure they have a longer asset life with less operational downtime.
More from our Knowledge Hub
- News
Celebrating and supporting our veterans at the Forces in Business Awards 2025
- Insights
Rebuilding trust in water: Interim recommendations from the Independent Water Commission
- Insights
Mitigating the impact of the 4 ‘I’s to reduce pollution in water networks
- News
Esh Construction secures Northumbrian Water repairs and maintenance framework
Environmental compliance today, creating a sustainable tomorrow
Helping you reduce risk to the environment and your operation by managing assets compliantly while achieving commercial, ESG, and net-zero goals.
Contact our experts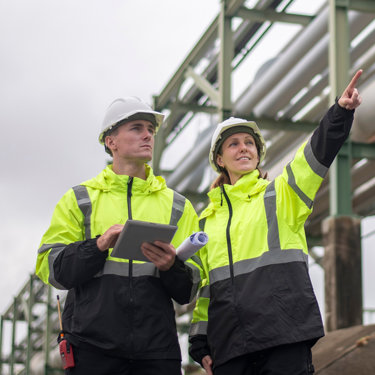