Repair and spray lining of storage tank bund system at gas terminal
Published: 10 March 2020
The project
Adler and Allan was tasked with the maintenance and repair of an interconnecting tank bund system used for tanks containing Natural Gas and Meg condensate liquid and vapour at Bacton Gas Terminal. Works had to be carried out on a large system, consisting of eight bunds, each with an internal area size averaging 500 square metres, divided by dwarf walls. Strict legislation covers safe working practices at gas terminals. There cannot be any risk of sparking, so strictly no ignition sources are permitted at any gas terminal site. All equipment used has to be ATEX rated, which ensures that if a spark is ignited, there is no risk of explosion.
The solution
Due to the nature of the contents of the tanks, Adler and Allan sought specialist advice when deciding on the lining material. The polyurea lining system, HT100FB, was selected by our consultants as the most suitable material. Perenco also carried out their own independent investigations of the suitability of HT100FB, looking into a range of processes including cleaning, prepping, overbanding and priming. Once the lining had been given the go-ahead, Adler and Allan teams set to work installing HT100FB in each bund over a series of programmed works. Initial preparation included cleaning, prepping, replacement of the construction and movement joints, and remedial concrete repairs. Backing rods were inserted where needed, covered with EPL9, primed and gritted for overbanding. On one of the tanks, bleach had to be flushed off the bund using a jet washer. Before the spray lining was applied, all equipment was masked off to protect it from any overspray. Adler and Allan teams also had to overcome certain obstructions in order to get the spray lining on effectively: there were pipes in the way, cable trays had to be removed from flank walls, and heights had to be adjusted to make way for the equipment. All Adler and Allan equipment taken on to site was ATEX rated, from personal protective equipment through to batteries and power tools. The spray trailer was modified to comply with site safety rules by fitting a Chalwyn Valve and Spark Arrestor to stop any ignition sources. An ATEX rated Spray Rig was purchased for the contract, which will also enable Adler and Allan to undertake similar works at hazardous environments. Additional safety measures included adopting a sign-in and out system to ensure all workers were accounted for at all times.
The outcome
Working close to the shoreline of the North Sea meant the Adler and Allan team faced testing weather conditions whilst carrying out the contract. The unpredictable nature of a gas terminal meant time was also an issue – when an evacuation alarm sounded an immediate exit from the work area was required and a return to work could not take place until safe to work clearance was given. Despite this, each bund took only 15 days to complete. The four completed bunds have now passed independent validation, which is an excellent achievement. The job has been a success, and as a result, Adler & Allan has been awarded similar work at other gas and oil fields and not limited to fuel chambers etc. on MOD sites.
More from our Knowledge Hub
- News
Two prestigious wins at Water Industry Awards and Women in Utilities Awards 2025
- News
Celebrating and supporting our veterans at the Forces in Business Awards 2025
- Insights
Rebuilding trust in water: Interim recommendations from the Independent Water Commission
- Insights
Mitigating the impact of the 4 ‘I’s to reduce pollution in water networks
Environmental compliance today, creating a sustainable tomorrow
Helping you reduce risk to the environment and your operation by managing assets compliantly while achieving commercial, ESG, and net-zero goals.
Contact our experts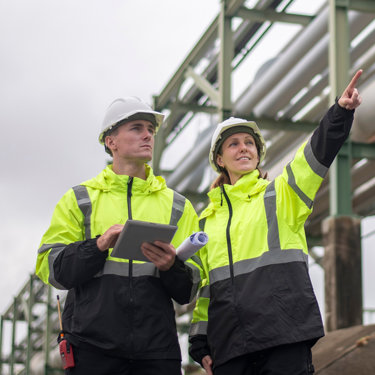