HFO spill response, Southampton Docks
Published: 21 February 2024
The problem
As an accredited Marine Oil Spill Response Organisation (OSRO) and the port’s Tier 2 contractor, Adler and Allan were mobilised by a Port Agent to provide decontamination and management of hazardous waste services following a spill of Heavy Fuel Oil (HFO) onboard a container ship which was berthed at Southampton Docks.
The spill was confined to the under-deck cargo hold, with no impact to the marine environment or quayside.
Adler and Allan’s initial scope of work was to assess the situation, taking remedial actions so that the vessel and port could continue with loading operations as soon as possible and to arrange for safe disposal of all contaminated materials as hazardous waste.
Adler and Allan’s Head of Response Services attended the vessel to further assess the situation and outline a response strategy with the Captain and Marine Superintendent of the vessel.
The volume of spilled HFO was initially estimated at over 5m3 by the Marine Superintendent, based on an estimated depth of 0.02m across the contaminated areas in Bays 34 and 38.
It was agreed that the use of a road vacuum tanker/jetting unit would be the most appropriate means by which to remove the gross product (Stage 1 Decontamination), followed by further manual recovery of stranded oil (Stage 2 Decontamination) and final polish (Stage 3 Decontamination) operations to remove as much staining as possible and any secondary contamination of ladders, walkways, handrails etc.
During Stage 1 Decontamination Operations, this initial estimate was revised to 10-12m3 by the response team on site.
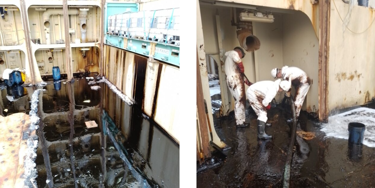
The solution
- Following security checks and site safety induction, a Risk Assessment Method Statements (RAMS) for shipside decontamination operations was submitted to the port operator for review and approval as part of a Safe System of Work. Subsequently a Permit to Work (PTW) was issued covering the next two days including the bank holiday Monday.
- All contaminated solids were recovered to open top Intermediate Bulk Carriers (IBCs) for temporary storage and onward disposal. These were then loaded onto a 40ft FR and removed using the shoreside gantry crane.
- All waste was segregated and treated in line with the principles of the waste hierarchy and regulatory guidance.
- Where possible (subject to port operations/crane availability), all response personnel gained access to the hold via a man riding cage, otherwise access/egress was via a number of ladders.

The results
- Technical Advisor was on site within 2hrs of mobilisation.
- Solid hazardous waste generated during the operations was double bagged to minimise the risk of leakage before being placed into open top IBCs. The IBC’s not only provided a suitable container for onward transport but also acted as a bund, further reducing the risk of secondary contamination. Post oil recovery, Adler and Allan completed a decontamination process of all contaminated equipment and PPE. Adler and Allan consulted with the Captain and Ships Agent on completion of the works to ensure a satisfactory conclusion before providing a post spill report in the following days.
- No release of product to the environment during recovering operations.
- No lost time safety incidents through the duration of the project
“We appreciate great job done by your team in such a short time… looking forward to cooperate with you on other projects. Thank you very much!”
Captain / Superintendent - Port Agent
More from our Knowledge Hub
- Case study
Decommissioning and redeveloping a mechanical transport fuel installation at Sennybridge Training Area
- News
Two prestigious wins at Water Industry Awards and Women in Utilities Awards 2025
- News
Celebrating and supporting our veterans at the Forces in Business Awards 2025
- Insights
Rebuilding trust in water: Interim recommendations from the Independent Water Commission
Environmental compliance today, creating a sustainable tomorrow
Helping you reduce risk to the environment and your operation by managing assets compliantly while achieving commercial, ESG, and net-zero goals.
Contact our experts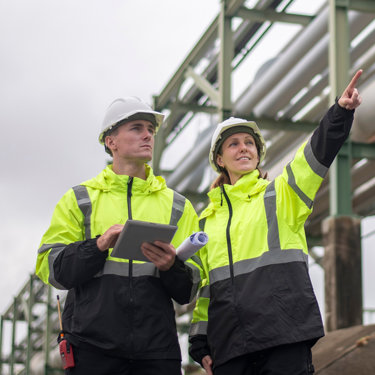